A typical residential garage floor should be at least 4 inches thick. For commercial or heavy-duty use, a thickness of 6 inches is recommended.
Determining the proper thickness for a garage floor is crucial for its longevity and durability.
A garage floor’s thickness directly impacts its ability to withstand the weight of vehicles and resist cracking under pressure. For most home garages, a 4-inch thickness strikes the right balance between strength and material cost.
This offers sufficient support for everyday cars and light storage without overbuilding. For those using their garages for heavier vehicles or as workshops with heavy equipment, opting for a 6-inch thick concrete slab provides additional support to handle the increased load.
Carefully choosing the right thickness ensures your garage floor can stand up to its intended use while providing a solid, long-lasting surface.
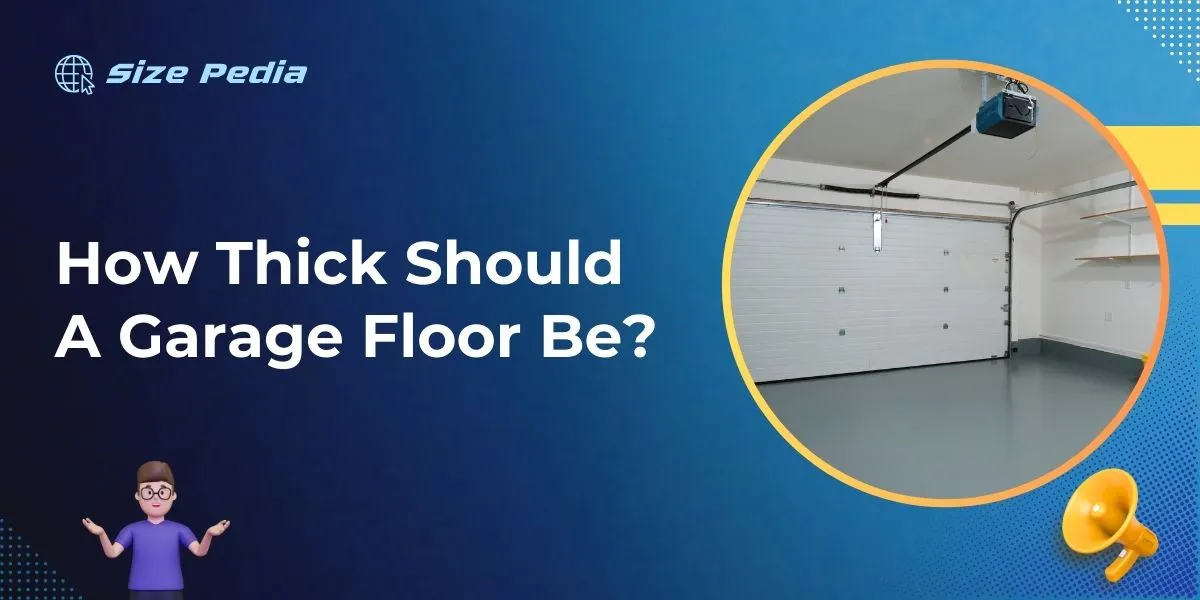
Ideal Thickness For Garage Floors
Deciding on the ideal thickness for your garage floor is crucial for its longevity and durability. The right thickness ensures the floor can withstand daily wear and tear, heavy vehicles, and mechanic work. Let’s explore the key factors and standards that dictate how thick a garage floor should be.
Factors Influencing Thickness
Several variables play a role in determining the proper garage floor thickness. These include:
- Vehicle weight: Heavy machinery demands a thicker slab.
- Usage frequency: Regular vehicle traffic can affect the floor’s integrity.
- Climate: Regions with frost heave require thicker floors to prevent cracking.
- Soil type: Poor soil conditions often necessitate a thicker floor for added support.
- Reinforcement: The presence of rebar or wire mesh can affect the thickness.
Minimum Thickness Standards
For a standard residential garage, minimum recognized thickness is 4 inches. Important specific considerations include:
Type of Use | Minimum Thickness |
Residential Garage | 4 inches |
Commercial Garage | 6 inches or more |
Industrial Garage | 8 inches or more |
Keep note, for enhanced performance and strength, exceed these minimum recommendations whenever possible.
Material Choices That Impact Durability
Choosing the right materials is crucial for a durable garage floor. Materials impact a floor’s ability to withstand heavy use, temperature changes, and chemical spills. The longevity of your garage floor relies on proper material selection.
Concrete Grade And Composition
Concrete strength, quality, and mix design shape the garage floor’s durability. Use a high-quality concrete mix with a compressive strength of at least 4,000 psi for optimal results.
This can withstand heavy loads and resist cracking over time. The composition should include a well-graded blend of sand and aggregates, along with a water-cement ratio that ensures maximum strength and workability.
Reinforcement Options
To further strengthen your garage floor, consider adding reinforcements. Steel rebar or wire mesh can be embedded into the concrete to help bear the load and minimize cracking.
Synthetic or steel fibers are also popular; they disperse throughout the concrete, offering improved tensile strength and crack resistance. These materials are essential for a floor that can handle massive weights and high traffic without deteriorating.
Design Considerations For Longevity
Building a garage floor that stands the test of time demands smart design. It’s not just about pouring concrete. Think about the floor’s thickness. Why? Well, it helps your floor last.
It handles heavy cars or maybe storage. Let’s dive into some key design elements that add years to your garage floor’s life.
Slope And Drainage
Water is no friend to a garage floor. A flat floor may lead to puddles. Puddles cause problems. Setting a slight slope guides water to the drain. Now, that’s smart! A typical slope is about 1/8 inch per foot. You want to consider this:
- Use a gentle slope: Too much and you’ll feel it. It may cause things to roll away.
- Maintain proper drainage: This shields the floor from water damage. Less damage means a longer life for your floor.
Expansion Joints
Concrete shifts and moves. It’s just what it does. Consider expansion joints as a relief system for stress. They prevent cracks. They let the concrete breathe. Aim to place joints at least every 10 feet in each direction. This helps the garage floor flex and not break.
Surface Treatments
The top layer needs protection. Surface treatments offer that armor. Let’s look at some options:
Type of Treatment | Benefits |
Sealers | Block moisture, resist stains |
Epoxy coatings | Hardy, look great, easy clean |
Stains | Add color, do not fade fast |
Choose a treatment that fights off tire marks, oil spills, and chemicals. The right one can add shine and make cleaning a breeze.
Calculating The Load Capacity
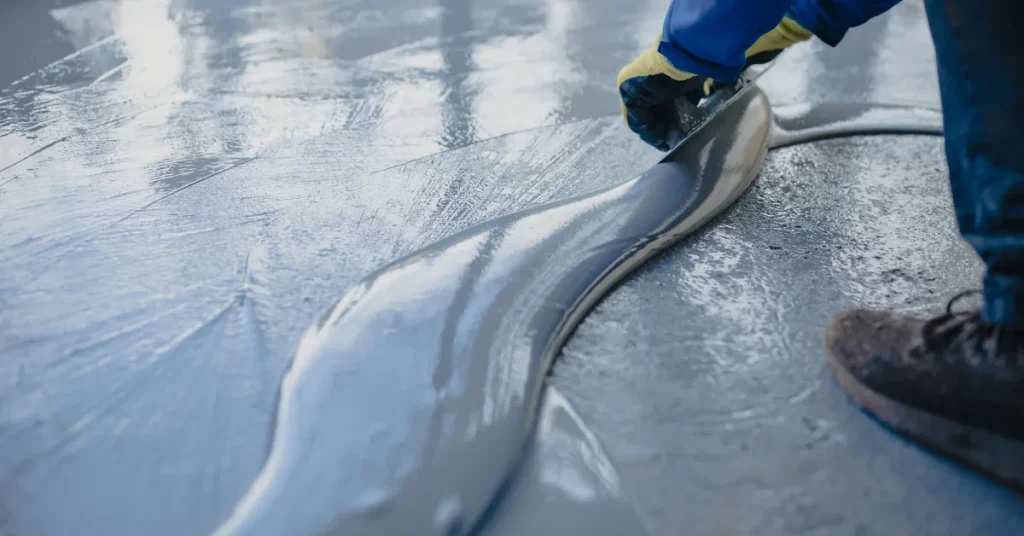
A crucial step in designing your garage floor involves calculating its load capacity. This is essential for the longevity and safety of the structure.
Vehicle Weight Factors
The weight of your vehicles plays a key role in determining the required thickness of your garage floor. Consider the following:
- Car Size: Small cars exert less pressure compared to larger vehicles.
- Vehicle Type: Trucks need thicker floors due to their heavier weights.
- Average Load: Include the weight of frequently transported goods.
Non-vehicular Load Considerations
Every garage floor must account for more than just cars and trucks. Note other loads:
- Storage Units: Shelves and cabinets add extra weight to the floor.
- Equipment: Heavy machinery requires additional floor support.
- Usage Frequency: Regular heavy use can impact the floor’s durability.
Ensure your floor can support all expected loads with a safety margin.
Vehicle Type | Minimum Thickness |
Passenger Vehicles | 4 inches |
Light Trucks | 5 inches |
Heavy Machinery | 6 inches or more |
Refer to local building codes and professional engineers when planning your floor.
Installation Best Practices
Embarking on the journey to install a sturdy garage floor, understanding the layers and steps is crucial for endurance and strength. Let’s dive into the best practices for a floor that stands the test of time and weight.
Ground Preparation
The foundation for any great garage floor is solid ground preparation. A poorly prepared base can lead to cracking and structural issues down the line. Follow these steps:
- Remove debris and ensure the soil is compact.
- Ensure the sub-base is level and uniformly compact.
- Add a layer of gravel and compact it again for optimal drainage.
Pouring Technique
Accuracy in the pouring process secures a level and robust garage floor. Pay attention to these pointers:
- Concrete mix must be consistent throughout the pour.
- Use a gauge rake to spread the concrete evenly.
- Level the surface with a screed and smooth it out with a trowel.
Curing Time
A crucial step that often goes overlooked is the curing. Manage this final stage well by:
- Maintaining a moist surface for at least 7 days.
- Avoiding any traffic on the floor for up to 28 days.
- Temperature control is key to ensure optimal curing.
Maintenance To Preserve Garage Floor Integrity
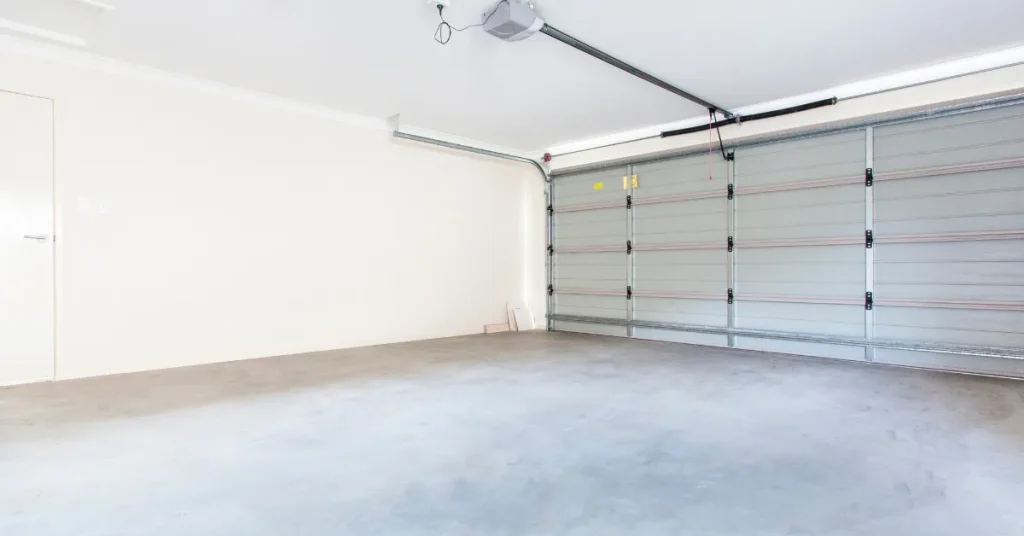
Keeping a garage floor in top shape goes beyond just considering its thickness. Proper maintenance is key to preserving the integrity of any garage surface.
From regular cleaning to addressing potential damage, a well-maintained floor can resist wear and tear, enduring the heavy loads and chemical spills it’s often exposed to. Follow these simple steps to safeguard your garage floor’s durability and appearance.
Regular Cleaning
Clean floors last longer. Dirt and grit can cause scratches. Spills can stain. To keep a floor strong, sweep it weekly. Use a mop or scrubber for deeper cleaning every month. A clean floor reduces wear.
Sealing And Protective Coatings
Sealants protect floors from moisture and stains. A sealant or epoxy coating adds a layer of defense. This barrier prevents damage from oil, grease, and chemicals. Apply a new coat every few years for optimal protection.
Addressing Cracks And Damage
Fix cracks fast to avoid bigger problems. Small cracks can grow. Inspect the floor regularly for any signs of damage. Use a concrete filler or sealer to repair minor cracks. For larger issues, consult a professional.
- Clean spills immediately to prevent stains.
- Check the sealant’s condition during cleaning.
- Inspect for cracks and repair them swiftly.
Maintaining the floor extends its life. A thick garage floor is just the beginning. Good maintenance practices preserve its integrity for years.
FAQs About How Thick Should A Garage Floor Be
How Thick Is A Standard Garage Floor?
A standard garage floor typically measures around 4 inches (10 cm) in thickness for residential use.
How Thick Should A Concrete Garage Base Be?
A standard concrete garage base should typically be at least 4 inches (100mm) thick. For heavier vehicles or loads, increase the thickness to 6 inches (150mm).
Do You Need Rebar In A Garage Floor?
Rebar is recommended for garage floors to enhance strength and prevent cracking. It supports the concrete under heavy vehicle weight and temperature changes.
Do I Need A 4 Or 6 Inch Concrete Slab For Garage?
A 4-inch concrete slab typically suffices for residential garages. Opt for a 6-inch slab for heavier vehicles or commercial use.
Conclusion
Determining the ideal thickness for your garage floor hinges on usage and vehicle weight. Aim for at least 4 inches of reinforced concrete to ensure durability.
Proper installation and quality materials will provide a sturdy surface, enduring daily wear with ease.
Remember, investing in a strong foundation pays off long-term, safeguarding your garage’s structural integrity.
Resources:
1. https://basc.pnnl.gov/resource-guides/floor-above-garage