Epoxy flooring thickness varies from 0.2 mils for a coating to over 250 mils for a heavy-duty application. Standard commercial-grade epoxy floors are typically 2 to 3 millimeters thick.
Epoxy flooring presents a versatile and durable solution for both commercial and residential spaces, offering resistance to wear and chemical corrosion.
Its thickness can be tailored to the specific needs of the environment, making it ideal for a wide range of uses, from light traffic areas to heavy industrial zones.
One of the key advantages of epoxy is its ability to bond to concrete, which provides a seamless and robust surface.
Epoxy floors are not only durable but also offer an aesthetic appeal, with a variety of colors and patterns available. Choosing the right thickness and composition of an epoxy floor ensures long-lasting performance and protection for the underlying surface.
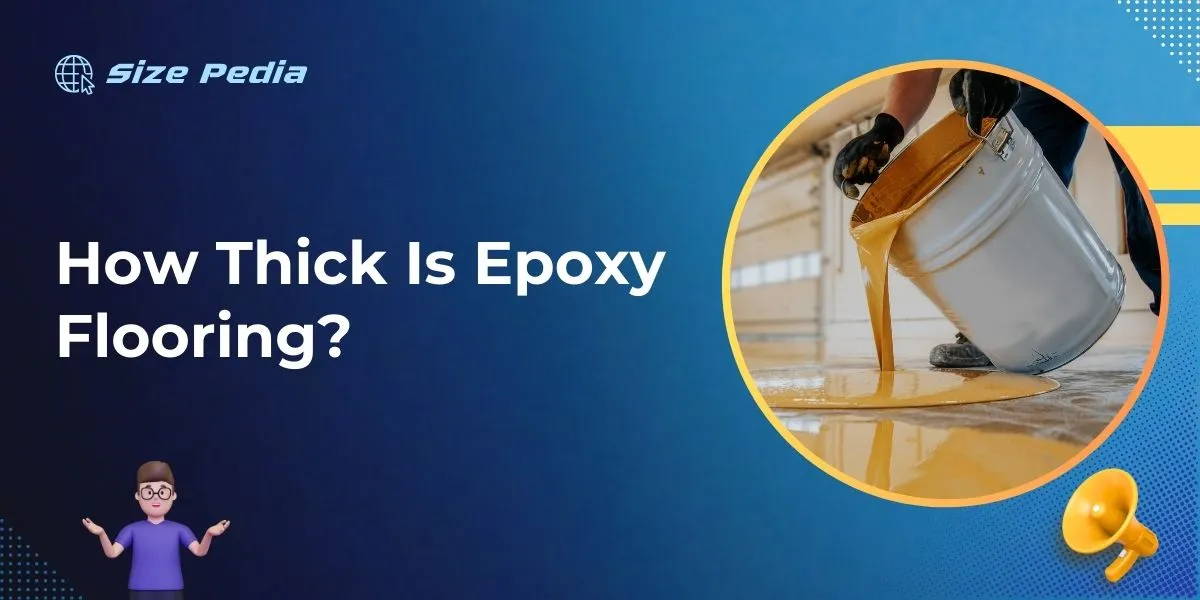
Introduction To Epoxy Flooring Thickness
Introduction to Epoxy Flooring Thickness is where we dive into the essential aspects of epoxy flooring. Not all floors are equal; the thickness of epoxy coatings can hugely impact their performance and durability.
Understanding the range of thicknesses and their purposes helps in making an informed decision for flooring projects.
What Is Epoxy Flooring?
Epoxy flooring is a type of surface coating that will transform a floor from plain to high performing and durable.
It consists of a system that involves applying a layer of epoxy resin over a substrate, which usually is concrete. Epoxy floors are known for their resilience and glossy finish.
Importance Of Thickness In Flooring Durability
The thickness of an epoxy floor often dictates its ability to withstand various conditions. Floors with greater thickness are generally capable of handling heavy traffic and resisting damage from chemicals or spills.
Each extra millimeter in thickness can provide a substantial boost to the floor’s longevity and protection.
- Self-leveling epoxy: typically 2-3 mm for commercial areas
- High-build epoxy: 4-5 mm for industrial zones with heavy loads
- Epoxy mortar systems: up to 5 mm for maximum impact resistance
Factors Determining Epoxy Floor Thickness
When choosing epoxy flooring, thickness is a key factor. This choice influences durability, appearance, and performance. Various elements dictate how thick your epoxy floor should be. Understanding these factors ensures a robust and lasting surface.
Types Of Epoxy Resin Systems
Not all epoxy systems are equal. They vary in composition and purpose. The basic types include:
- Water-Based Epoxy: Thin, often used for priming.
- Solvent-Based Epoxy: Medium thickness, versatile.
- 100% Solids Epoxy: Thick, durable, for heavy-duty use.
Each type sets to a different thickness range. A professional assessment helps select the right system for your needs.
Intended Use And Traffic Levels
How you use your space impacts floor thickness. Consider the following:
- Light Traffic: A thin coat may suffice.
- Medium Traffic: A thicker layer for durability.
- Heavy Traffic: The thickest option for resilience.
Garages, warehouses, and industrial areas often require thicker epoxy to withstand use.
Substrate Conditions
The existing floor condition matters. Note these points:
- Smooth Surfaces: May need less epoxy.
- Uneven Floors: Require more material for level coverage.
- Damaged Concrete: Sometimes a thicker layer is necessary to cover imperfections.
A qualified installer can evaluate the substrate and recommend the appropriate epoxy thickness.
Standard Measurements Of Epoxy Layers
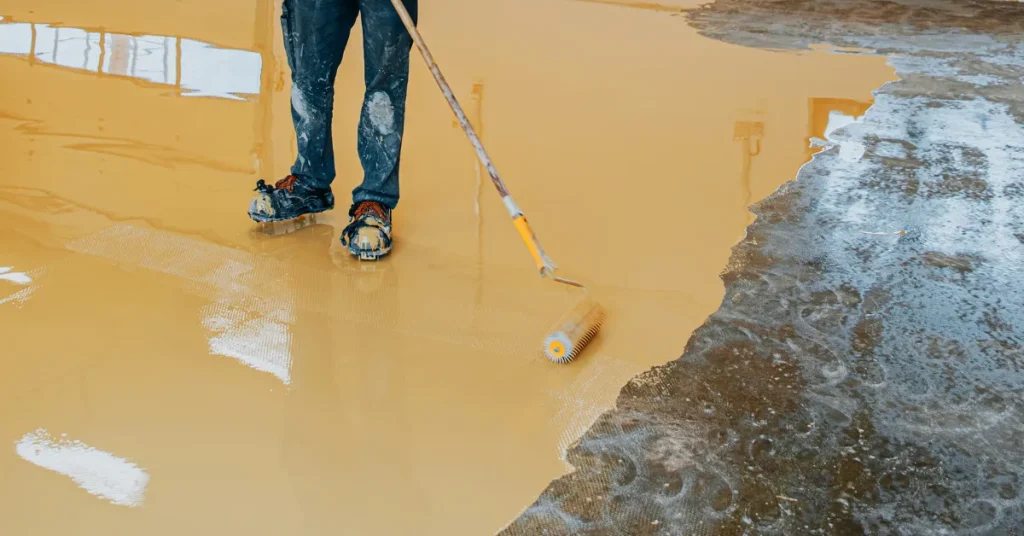
Epoxy flooring boasts a versatile range of thickness levels. Each layer serves a unique purpose. The thickness of the epoxy often decides its function. Proper measurement is key to its durability and effectiveness.
Thin-film Epoxy Coatings
Thin-film epoxy coatings are the lightest layers. They are perfect for simple applications. Think of them as the epoxy’s featherweight class. They usually measure:
- 4 to 6 mils (0.004 to 0.006 inches) per layer.
- Great for basic floor protection.
- Used in residential settings or light-traffic areas.
Self-leveling Epoxy Applications
Self-leveling epoxy is middleweight. It forms a smooth finish. It works well for uneven surfaces. The standard thickness ranges:
- 1/16-inch to 1/8-inch for normal use.
- Builds a flat layer over old or new concrete.
- Suits commercial or manufacturing spaces.
Mortar Epoxy For Industrial Use
The heavyweight champion is the mortar epoxy. It’s designed for the toughest environments. It’s the thickest type available. Common measurements include:
Application | Thickness |
High-traffic industrial | 3/16-inch to 1/4-inch |
Areas needing repairs | 1/4-inch to 1/2-inch |
Mortar epoxy withstands heavy equipment. It’s ideal for warehouses and garages.
Calculating Required Thickness For Your Floor
Embarking on your epoxy flooring journey starts with understanding the thickness required.
Assessment Of Environmental Impact
Before selecting an epoxy coating, the environment must get a thorough assessment. Different factors play a crucial role:
- Temperature fluctuations – They affect epoxy curing and performance.
- Humidity levels – High moisture can impair bond strength.
- Chemical exposure – Certain chemicals demand thicker layers for protection.
Load-bearing Considerations
Flooring should bear the weight of daily operations:
- Foot traffic – Less thickness needed for light use.
- Vehicle traffic – Heavier loads need more epoxy.
- Equipment weight – Consider the weight of machines and any potential impact.
Load Type | Recommended Thickness |
Light Foot Traffic | 1-2 mm |
Heavy Machinery | 3-5 mm |
Professional Thickness Recommendations
Experts provide tailored advice for optimal performance:
- Evaluate the purpose of your space.
- Consider the daily operational load.
- Get a personalized thickness proposal.
Contacting professionals is crucial. They ensure your floor meets both durability and safety standards. Consistent communication with experts achieves the best results.
Installation Process And Achieving Desired Thickness
The installation process and achieving the desired thickness of epoxy flooring is as much an art as it is a science. Understanding the correct installation procedures ensures not only aesthetic appeal but also longevity and durability.
Surface Preparation Steps
Before applying epoxy, a clean and smooth surface is critical. The following steps will guide you through the process:
- Remove Old Coatings: Strip any existing paints or sealers to expose the bare concrete.
- Clean the Surface: Get rid of dirt, grease, and other contaminants.
- Repair Cracks: Fill in any cracks or chips in the concrete for an even surface.
- Profile the Concrete: This ensures the epoxy adheres well to the surface.
Application Techniques For Uniformity
Epoxy must be applied carefully to avoid uneven areas. Use these techniques:
- Ensure Level Application: Use gauges or notched squeegees for consistent thickness.
- Use High-Quality Tools: Good rollers and squeegees reduce air bubbles and assist in even spread.
- Apply in Sections: Divide the floor into sections for focused application.
Quality Control During Installation
Diligent quality control is vital. Follow these steps for best results:
- Monitor Thickness: Regularly check to keep the thickness uniform.
- Watch for Defects: Address any air bubbles or imperfections immediately.
- Avoid Contamination: Keep the area clean to prevent debris in the epoxy.
- Control Environment: Temperature and humidity impact curing and should be managed.
Maintaining Epoxy Floor Thickness Over Time
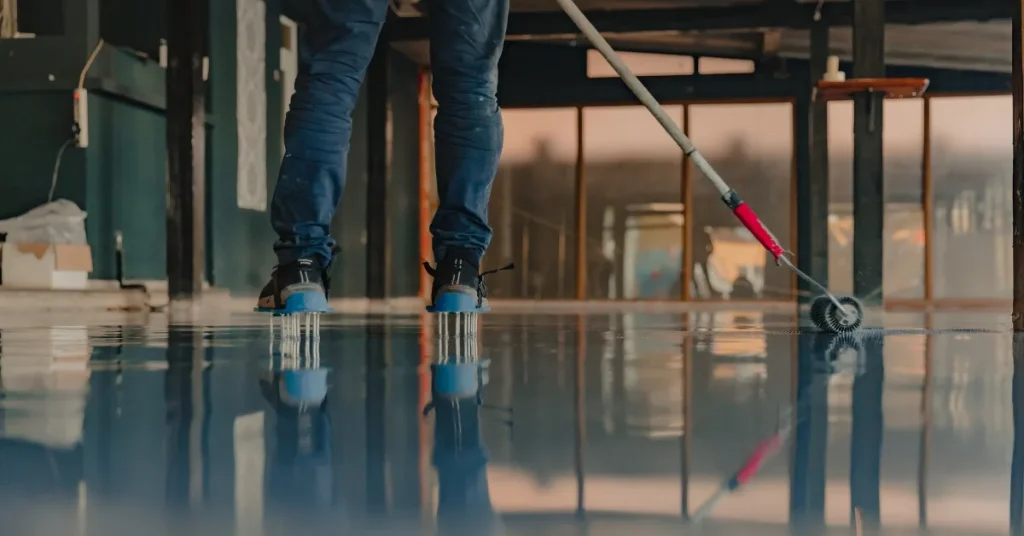
Maintaining epoxy floor thickness ensures longevity and performance. This durable flooring solution can last for years. Proper care keeps it strong. Consider these maintenance steps:
Routine Maintenance Tips
- Clean regularly to prevent dirt buildup.
- Use proper cleaning solutions that are safe for epoxy.
- Avoid harsh chemicals that can damage the surface.
- Apply a topcoat every few years to protect the layer beneath.
Dealing With Wear And Tear
- Inspect the floor for scratches or chips regularly.
- Perform small repairs promptly to prevent further damage.
- Place mats in high-traffic areas to reduce wear.
- Use soft rubber wheels on heavy equipment to decrease gouges.
When To Consider Resurfacing
Resurfacing may become necessary over time. Look for these signs:
Signs | Action |
Discoloration | Assess for resurfacing need. |
Surface unevenness | Plan for professional evaluation. |
Peeling or flaking | Seek resurfacing options. |
Contact a professional when the floor shows wear or damage signs.
FAQs About How Thick Is Epoxy Flooring
How Thick Is A Typical Epoxy Floor?
A typical epoxy floor coating ranges from 2 mm to 3 mm in thickness. More heavy-duty applications may require thicknesses up to 5 mm or more.
Is Epoxy Floor Paint Thick?
Epoxy floor paint typically has a thicker consistency than standard paint, providing a durable and robust coating for floors.
How Thick Is Self Leveling Epoxy?
Self-leveling epoxy typically has a thickness ranging from 1 to 3 mm when applied. The exact thickness can vary based on the product and application requirements.
Do Epoxy Floors Crack?
Epoxy floors are highly resistant to cracking, but they can develop cracks if the underlying concrete substrate moves or settles. Proper installation and maintenance reduce the likelihood of cracking.
Conclusion
Understanding the thickness of epoxy flooring suits various needs, from residential projects to industrial settings. The standard range is between 2 to 3 millimeters, ideal for durability and aesthetics.
For heftier demands, consider specifications up to 10 millimeters. Your choice is pivotal for long-lasting, splendid floors.
Plan wisely for optimal results.
Resources:
1. https://www.cfm.va.gov/til/room/roomFinishes.pdf