A military submarine’s hull typically ranges from 1.5 inches (3.81 cm) to about 3 inches (7.62 cm) thick. This thickness ensures both the vessel’s structural integrity and its ability to withstand high water pressure at depth.
Submarine hulls play a critical role in naval defense and oceanic research, designed to endure the extreme conditions underwater.
The hulls are composed of high-strength steel or titanium, allowing submarines to dive to great depths and operate in the harshest of environments.
Navigating the depths requires a vessel that not only protects those on board but also successfully resists the immense pressure exerted by the ocean’s weight. Engineers meticulously craft these vessels to optimize durability, stealth, and performance.
Understanding the specifications of a submarine’s hull can reveal much about its capabilities, including maximum depth range and potential for stealth.
As technology advances, the precision in the design and construction of submarine hulls continues to play a pivotal role in maritime engineering.
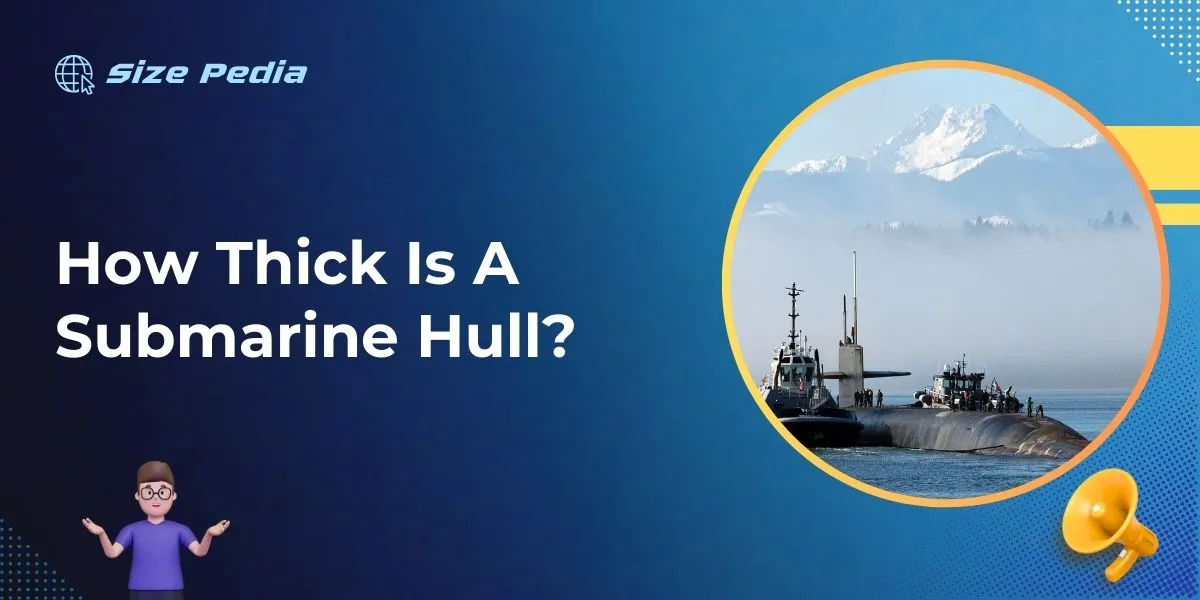
The Essence Of Submarine Hull Thickness
The Essence of Submarine Hull Thickness plays a vital role in the functionality and safety of submarines. The hull, a submarine’s outer shell, faces extreme underwater pressures.
Its thickness is not just about withstanding the ocean’s might but also about ensuring the submersible can surface and dive smoothly. This balance is crucial for the vessel’s optimal performance and the crew’s survival.
Balancing Buoyancy And Durability
A submarine’s hull is a marvel of engineering. It must be durable enough to resist the crushing force of water, yet not so heavy that it cannot float.
Thick steel plates are used in constructing the hull, which must be carefully calculated to maintain buoyancy.
The hull’s design allows it to withstand considerable external pressure while being light enough to control ascent and descent in water.
- Pressure increases as depth increases.
- Hull thickness must counteract this pressure.
Materials That Withstand Ocean’s Pressures
A variety of advanced materials contribute to the hull’s integrity. High-strength steel alloys are commonly employed for their resilience and durability.
These materials undergo rigorous testing to ensure they can handle the extremes of undersea travel.
Material | Properties |
HY-80 Steel | High yield strength, good weldability |
Titanium | Exceptional strength-to-weight ratio |
Non-metallic Composites | Corrosion resistance, reduced weight |
Combined, these characteristics ensure the submarine’s hull remains impervious to the ocean’s relentless pressures. Regular maintenance and checks are essential, safeguarding the hull’s integrity over time.
Engineering Behind The Hull

The engineering of a submarine hull is a marvel of modern science and technology.
Submarine hulls must withstand extreme underwater pressure and provide a safe environment for crew and machinery.
The thickness of these structures is a testament to the ingenuity and precision of naval engineering.
Design Principles For Submersion
Submarine hulls are engineered with specific design principles to ensure they can submerge and resurface safely. Let’s delve into these core principles:
- Pressure Resistance: Hulls must resist crushing from the water’s pressure.
- Buoyancy Control: Submarines use ballast tanks to sink and float.
- Minimized Turbulence: Sleek designs reduce drag and conserve energy.
Innovations In Submarine Architecture
Submarine hull advancements showcase incredible innovations in naval design. Here are some key developments:
- Hybrid Materials: New composites combine strength with lighter weight.
- Enhanced Stealth: Special coatings reduce acoustic signatures.
- Modular Construction: Improved build methods enhance repairability.
Comparing Military And Civilian Subs
Did you ever wonder about the hull thickness of submarines? Let’s dive into the differences between military and civilian subs.
Differing Design Requirements
The design of submarine hulls varies greatly between military and civilian vessels. Military submarines must withstand deep-ocean pressures and potential combat scenarios.
In contrast, civilian subs often focus on scientific research or tourism. Their design prioritizes visibility and comfort over defense capabilities.
Case Studies: Nuclear Subs Vs. Research Subs
Nuclear submarines represent the pinnacle of military engineering, designed to operate silently and remain submerged for months.
Research submarines, however, serve a different purpose. They support oceanic exploration and collect data on marine life and underwater geography.
Submarine Type | Hull Composition | Hull Thickness | Primary Use |
Nuclear Sub | High-strength steel alloy | Several inches | Military operations |
Research Sub | Titanium or Transparent Acrylic | Varies; Often less than military subs | Scientific exploration |
Nuclear subs’ hulls need to endure intense underwater pressures and explosive impacts. Their hulls are often much thicker than those of civilian subs.
Research vessels rely on lighter materials like titanium, making them more maneuverable for close observation of underwater features.
The Role Of Depth In Hull Design
Understanding submarine hull design is key to appreciating these incredible machines. Deep below the ocean’s surface, immense pressure tests the limits of human engineering. Let’s dive into how depth plays a crucial role in shaping submarine hulls.
How Depth Influences Thickness
Submarine hulls must withstand great pressures. As a sub dives deeper, the water pressure on its hull increases.
This pressure can crush a hull that’s not strong enough. Engineers use special materials and designs to make sure submarine hulls can handle this pressure.
- Thicker hulls for deeper dives: A deeper dive requires a thicker hull to resist the increased pressure.
- Material matters: Subs use steel or titanium for strength. This choice is crucial for a sub’s ability to dive deep.
- Precision in manufacturing: Even a tiny flaw can be dangerous. Subs are made with great care to avoid any weak spots.
Record-breaking Dives And Hull Considerations
Some subs make history with their depth capabilities.
The deeper a submarine goes, the more impressive its engineering. Record-breaking dives push the limits. They prove the power of human design.
Submarine | Max Depth | Hull Thickness |
Trieste | 10,911 meters | 12.7 cm |
Seawolf-class | 610 meters | 3.8 cm |
Each record dive leads to new discoveries. These lead to improvements in submarine hulls. Engineers learn and create even stronger, thicker hulls for future subs.
Maintenance And The Longevity Of Submarine Hulls
The hull of a submarine is its shell. It faces the sea’s harsh life. Good care makes hulls last long. We will explore how the deep sea affects hulls. And how we keep them in top shape.
Corrosion And Wear In The Deep Sea
Submarines face many challenges underwater. Saltwater and pressure can damage them. This damage is corrosion. And wear is from moving parts touching. Together, they can weaken a submarine hull.
Techniques For Prolonging Submarine Life
To help submarines last longer, experts use special methods. They pick strong materials. They also do regular checks. And they fix small problems fast. All these keep submarines safe.
- Inspection: Crews check for damage often.
- Materials: Use corrosion-resistant stuff.
- Coatings: Protective layers guard the hull.
- Repairs: Fix issues right away.
Future Trends In Submarine Design

As the depths of the oceans beckon, submarine design continues to evolve. Engineers and designers seek to make these undersea vessels safer, stronger, and more versatile. They embrace new technologies and materials.
The future of submarine design looks as mysterious and promising as the deep blue itself. Let’s dive into the upcoming trends that may redefine the aquatic frontier.
Advancements In Material Science
The hull’s thickness plays a crucial role in a submarine’s performance. It must withstand immense underwater pressure. In response, material science steps forward.
Future submarines may feature composite materials that surpass traditional steel in strength and resilience. These materials could reduce weight yet increase structural integrity.
- Nanocomposite structures
- Carbon fiber-reinforced polymers
- Titanium alloys
Researchers are testing these to push the limits of submarine hulls. Stronger materials equal deeper dives with less risk.
Eco-friendly Innovations And Submarine Hulls
Sustainability strikes a chord in all sectors, and submarines are no exception. Environmental responsibilities shape design trends.
Future submarine hulls might incorporate materials or coatings to reduce ocean noise. This could protect marine life from harmful disruptions caused by submarines.
Electric propulsion systems offer quieter, cleaner journeys through the ocean’s depths. Innovators also explore the use of renewable energy sources.
Solar panels or underwater turbines could power subs while preserving ocean habitats.
New tech aims to make submarines greener and kinder to their underwater environment.
FAQs About How Thick Is A Submarine Hull
How Thick Is A Us Submarine Hull?
The hull thickness of a US submarine varies but generally ranges between 1. 5 to 3 inches (3. 81 to 7. 62 cm).
How Thick Are Submersible Hulls?
Submersible hull thickness varies, typically ranging from 2 inches for deep-sea vessels to 4-5 inches for military submarines.
What Is The Best Material For A Submarine Hull?
High-strength steel alloys are optimal for submarine hulls, offering durability and withstanding extreme pressures deep underwater. Titanium is another excellent material, prized for its strength-to-density ratio and corrosion resistance, despite being costlier.
What Are Military Submarine Hulls Made Of?
Military submarine hulls are primarily made of high-strength steel, titanium, or a combination thereof to withstand deep-sea pressures.
Conclusion
Understanding the complexities of submarine hull thickness is essential for appreciating these underwater marvels.
Typically, modern submarines boast hulls up to several inches thick, providing the required strength and pressure resistance.
As innovation propels forward, so does the engineering marvel of submarine design, ensuring safety and functionality in the unyielding depths of the ocean.
Resources:
1. https://www.navy.mil/Resources/Fact-Files/Display-FactFiles/Article/2169558/attack-submarines-ssn/