A plasma cutter can typically cut metal up to 2 inches thick. This capability, however, largely depends on the machine’s model and power settings.
Plasma cutting technology offers a convenient and efficient solution for slicing through various conductive metals such as steel, aluminum, and copper.
This versatile tool harnesses the power of an accelerated jet of hot plasma directed at the metal, providing precision and speed for industrial, fabrication, and hobbyist applications alike.
The machine’s power supply and the size of the nozzle determine the maximum cutting thickness.
For businesses and DIY enthusiasts, understanding a plasma cutter’s abilities is critical to ensure clean cuts and optimal performance.
Selecting the right plasma cutter requires considering the types of materials you plan to cut and their respective thicknesses to meet your project’s demands successfully.

Unveiling The Power Of Plasma Cutters
Imagine cutting through metal like butter. That’s what a plasma cutter does. It’s a powerful tool that slices through metal with ease.
Yet, many wonder about its limits. Just how thick can a plasma cutter cut? Let’s dive into the world of plasma cutters and find out!
The Mechanics Behind Plasma Cutting
Plasma cutting is a process that uses ionized gas. This gas turns into plasma at high temperatures.
Plasma conducts electricity and blasts through metal. The process is swift and accurate. It’s great for cutting steel, aluminum, and other metals.
Plasma cutters work by sending an electric arc through a gas. This gas goes through a narrow opening. The gas gets so hot that it enters the fourth state of matter, plasma. The metal melts, and high-speed gas blows the molten metal away. This leaves a smooth cut.
Factors Influencing Plasma Cutter Capabilities
Different factors affect how thick a plasma cutter can cut. These factors include:
- Power supply: A stronger power supply lets a plasma cutter cut thicker metals.
- Cutter type: There are various types, each designed for different thicknesses.
- Material type: Some metals are easier to cut than others.
- Cutting speed: Going slower may allow for cutting thicker materials.
- Gas type: Different gases might improve the cutting process.
Plasma Cutter Model | Maximum Cut Thickness | Ideal Cut Thickness |
Entry-Level Cutter | 1/4 inch | 1/8 inch |
Mid-Range Cutter | 1/2 inch | 3/8 inch |
Commercial Grade Cutter | 1 inch | 3/4 inch |
To conclude, plasma cutters are robust tools. They tackle a variety of thicknesses. By understanding the factors that impact their performance, users can maximize their cutting capabilities. Now, are you ready to see what a plasma cutter can do for your project?
Thickness Spectrum: Understanding Material Limits
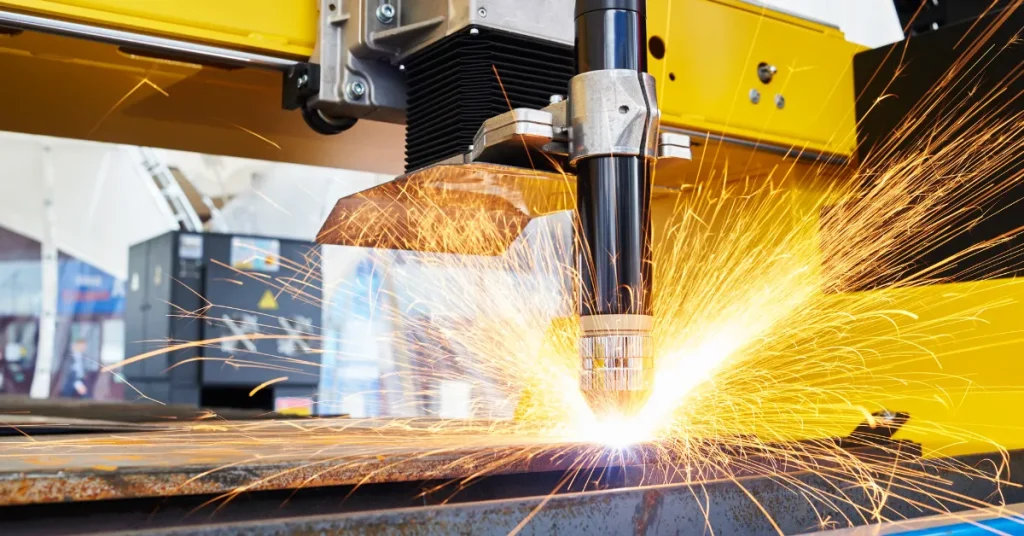
Plasma cutting has revolutionized metal cutting with its versatility. Knowing what thickness range a plasma cutter can handle is essential for both hobbyists and professionals alike. Before delving into specific numbers, it’s valuable to grasp what plasma cutting is.
A plasma cutter is a tool that passes an electrically conductive gas through a narrow opening at a high speed. This process creates a plasma that can cut through various metals with precision. The cutter’s effectiveness depends on the material’s thickness.
Typical Material Thickness Range For Plasma Cutting
Plasma cutters have a sweet spot for certain thicknesses where they perform best. Thinner materials cut more easily, with a smoother edge. Here’s what’s typical:
- Steel: up to 1 inch
- Stainless steel: up to 6/8 inch
- Aluminum: up to 2/8 inch
These ranges make plasma cutting ideal for a broad spectrum of projects.
The Upper Limits: How Thick Can We Go?
While plasma cutters excel with certain thicknesses, they are not unlimited in their capabilities. Users often wonder, how thick can a plasma cutter cut? The answer varies with technology advancements.
Material | Max Thickness | Typical Cutter |
Steel | 2 inches | High-Definition Cutter |
Stainless Steel | 1.5 inches | Conventional System |
Aluminum | 1 inch | Conventional System |
Cutting beyond these thicknesses may require more powerful, specialized equipment. Always ensure the cutter’s specs match the project demands.
Maximizing Cutting Potential
Cutting through metal with precision and speed, plasma cutting stands out in the metal fabrication world. But to truly tap into its power, understanding how to maximize its cutting potential is key.
This is not just about turning it on and pushing through the metal. It’s about making smart choices and adjusting the right settings.
Choosing The Right Plasma Cutter For The Job
Selecting the ideal plasma cutter sets the stage for successful cutting. Different machines handle various thicknesses. A basic guide is:
- Low-amperage plasma cutters can handle up to 1/4 inch.
- Medium-amperage cutters reach up to 1/2 inch.
- High-amperage options slice through 1 inch or more.
Assess the material typically cut and choose a machine that exceeds that thickness. This ensures clean cuts without straining the cutter.
Optimizing Cutting Parameters For Maximum Thickness
Tweaking your cutter’s settings helps in achieving maximum thickness cuts. Here’s how to optimize your cuts:
Parameter | Adjustment | Result |
Air Pressure | Set to the recommended PSI | Better quality, deeper cuts |
Cutting Speed | Slow down for thick metal | Avoid incomplete cuts |
Power Setting | Maximize amperage | Handles greater thicknesses |
The right combination of speed, power, and air pressure means you can cut thick materials efficiently. Always refer to the cutter’s manual for the best parameters for different metal thicknesses.
A test cut beforehand can confirm your settings are spot-on. Perfecting these elements can push your plasma cutter to its limits, leading to top-notch results.
The Role Of Compressed Gases
Understanding the role of compressed gases in plasma cutting is crucial. These gases not only fuel the cut but also influence the cut’s depth and quality.
A plasma cutter’s capability is defined by various settings of the compressed gases it utilizes. Let’s take a closer look.
How Gas Selection Affects Cut Depth And Quality
The choice of gas in plasma cutting is vital to both performance and precision. Below are key points on how gases affect cutting:
- Air: Versatile, provides decent cut quality on mild steel.
- Oxygen: Enhances cut quality on mild steel, can increase cut depth.
- Nitrogen: Ideal for stainless steel and aluminum, delivers a smooth cut edge.
- Argon-Hydrogen Mix: Enables deep cuts on thicker materials, best for stainless steel and aluminum.
Mixing gases can also alter results:
- Argon and hydrogen mix increases cut capacity on thick metal plates.
- Air and oxygen mix offers a cost-effective balance of cut quality and speed.
Pressure Settings And Their Impact On Cutting Performance

Appropriate pressure settings are critical for optimal cutting. Below is how pressure variations can impact the plasma cutter’s performance:
Pressure Setting | Impact on Performance |
Low Pressure | May cause incomplete cuts, with reduced speed and precision. |
Optimal Pressure | Fosters a steady arc with clean, sharp cuts. |
High Pressure | Can lead to excessive dross, warping and reduced consumable life. |
Different materials require unique pressure settings:
- Thin metals = lower pressures.
- Thick materials = higher pressures for deeper penetration.
Monitoring and adjusting pressure ensure optimal cuts every time.
Troubleshooting Common Issues With Thick Cuts
When tackling thick materials with a plasma cutter, users often encounter specific challenges. Knowing how to address these obstacles ensures clean cuts and prolongs the life of your equipment.
Two troublesome issues—dross and slag formation, and edge angularity with warping—stand out. Let’s dive into effective troubleshooting strategies.
Dealing With Dross And Slag Formation
Dross and slag can cling to the underside of cuts, dampening the quality of your work. Here’s how to reduce these unwanted by-products:
- Adjust the speed: If your cut speed is too slow, it increases dross. Find your equipment’s sweet spot for optimal performance.
- Correct cutting height: Maintain the right distance between the torch and material to minimize slag.
- Refine the angle: An incorrect angle might cause more buildup. Always aim for a perpendicular approach.
- Optimize amperage: Matching amperage to material thickness is crucial. Refer to your machine’s manual for guidance.
After cutting, tools like scrapers or grinders can help remove any residual dross or slag.
Mitigating Edge Angularity And Warping In Thick Materials
Edge angularity and warping distort the preciseness of cuts. Let’s tackle these problems head-on.
- Control the heat: Excess heat can warp metal. Cut in stages if necessary to allow cooling.
- Use proper supports: Secure material effectively to prevent movement due to thermal stress.
- Adjust technique: Fast travel speeds can reduce warping and improve edge quality.
- Calibrate gas flow: The correct gas flow and pressure contribute to smoother edges.
Regular checks for machine calibration and torch condition are essential to avoid these issues.
FAQs About How Thick Can A Plasma Cutter Cut
What Is The Maximum Thickness That A Plasma Cutter Can Cut?
The maximum cutting thickness of a plasma cutter varies by model, typically ranging up to 2 inches for high-end industrial units.
What Is The Thickest Metal You Can Cut With A Plasma Cutter?
A plasma cutter can typically cut metal up to 2 inches thick, but, the exact capability depends on the machine’s power and specifications.
How Thick Of Steel Will A 40 Amp Plasma Cutter Cut?
A 40 amp plasma cutter typically cuts steel up to 1/2 inch thick effectively. For best results, maintain clean contact and steady motion during the cutting process.
How Thick Can A 100 Amp Plasma Cutter Cut?
A 100 amp plasma cutter typically cuts metal up to 1 inch thick efficiently, while maximum cut thickness can reach approximately 1. 5 inches.
Conclusion
Wrapping up, selecting the right plasma cutter is crucial for cutting efficiency. Thicker metals demand higher power and proper speed.
By understanding your project needs, you can ensure precise and clean cuts. Remember, a quality plasma cutter is an investment in your workmanship.
Choose wisely for optimal results.
Resources:
1. https://www.aoc.gov/explore-capitol-campus/blog/cool-tools-plasma-cutting-machine-matter-precision