Submarine walls are typically between 6.5 inches to 11 inches thick. They balance the need for internal space and external pressure resistance.
Submarine construction is a marvel of modern engineering, designed to withstand the immense pressures of the deep sea.
These vessels dive to depths where the water pressure exceeds several hundred atmospheres, making the strength and thickness of their hulls a critical feature.
The exact thickness varies depending on the submarine’s size, class, and purpose, whether for military or research usage. Durable materials like high-strength steel or titanium allow submarines to safely explore and operate underwater.
Their robust construction not only provides safety to the crew but also ensures the submarine’s structural integrity against natural and human-made underwater threats.
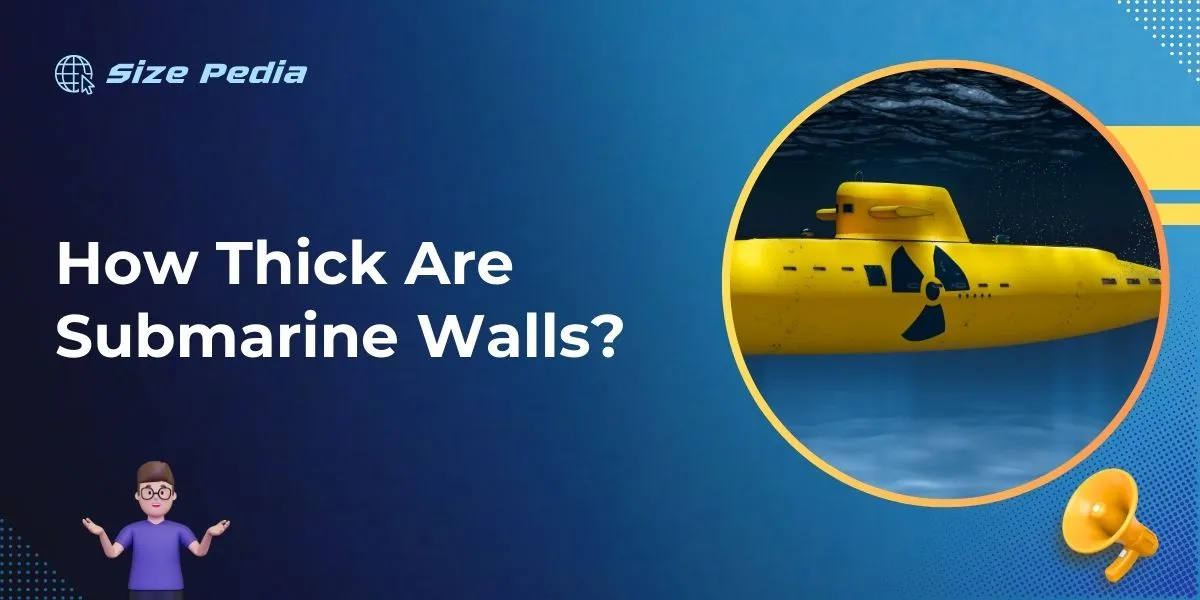
Submarine Wall Thickness: The Basics
Understanding submarine wall thickness is key to grasping how these vessels withstand deep-sea pressures.
Submarines feature walls engineered for extreme underwater environments. Here, we dive into what makes up these robust barriers of the deep.
Materials Used In Construction
The selection of materials is crucial for submarine integrity. Engineers use a mix of high-strength steel and other alloys for the hull.
These materials ensure a balance between flexibility and strength. They keep the vessel safe from high pressures and corrosive sea water.
- HY-80, HY-100, and HY-130 steels are common choices.
- Titanium alloys may be used for special, deep-diving subs.
Standard Thickness Range
The thickness of submarine walls can vary widely. Yet, there is a general standard. This ensures the structure can handle differing depths and pressures.
Sub Type | Wall Thickness |
Attack Submarines | 20 to 30 mm |
Ballistic Missile Submarines | Up to 250 mm |
Standard thickness ranges reflect the sub’s duty and depth goals. Attack submarines, with thinner walls, move faster. Ballistic missile submarines have thicker walls for deeper dives and protection.
- Surface vessel-resistant.
- Deep-diving capacities.
- Ballistic protection.
Pressure Challenges In The Depths
Submarines face immense underwater pressures that can crush objects as they dive deep. The walls of these vessels are expertly designed to withstand these forces.
As we explore how thick submarine walls are, we must first understand the incredible pressure challenges in the ocean’s depths.
Deep Sea Pressure Effects
The ocean’s pressure increases by roughly one atmosphere for every 10 meters of depth. This means submarines, some of which can dive several kilometers underwater, must be robust. The pressure effects in the deep sea are extreme.
Key points about deep sea pressure:
- Greater Depth, Greater Pressure: Pressure mounts quickly as a submarine descends.
- Consistent Force: This pressure acts evenly across the submarine’s surfaces.
- Compacted Volume: Under pressure, air-filled spaces become smaller.
Engineering For Extremes
Submarine walls are feats of engineering crafted to survive underwater extremes. Their thickness varies according to the submarine’s type and purpose.
Military submarines, including nuclear subs, boast some of the thickest walls. These walls must endure deep-sea missions and combat situations.
Research submarines, while also facing deep dives, often have specialized construction for their scientific tasks.
Let’s look at how engineers tackle the challenge of designing submarine walls.
Submarine Type | Typical Wall Thickness | Special Features |
Military | 6-11 inches | Designed to hold against explosions and enemy detection |
Research | 4-8 inches | Specialized for scientific instruments and deep-sea exploration |
Private | 3-6 inches | Luxury features with moderate depth capabilities |
Steel and titanium, materials known for their strength and durability, are common in submarine hull construction. Spherical shapes are often used for the deepest diving submarines due to the geometry’s even distribution of stress.
Design And Engineering: Behind The Hull
The design and engineering of submarine hulls are a showcase of modern ingenuity. The walls of these underwater behemoths are not just thick; they embody advanced science tailored to withstand the crushing pressures of the deep sea.
As we dive into the fascinating world of submarine hull construction, it’s clear that each layer serves a crucial role in ensuring the vessel’s durability, performance, and safety.
From Drafting To Reality
The journey from conception to construction of a submarine is fraught with challenges. It starts with meticulous planning and rigorous testing.
- Blueprint creation
- Material selection
- Prototype testing
Detailed 3D models transform into substantial steel structures. These models are vetted against the toughest conditions. The hull must be impenetrable, flexible, and safe. Computer simulations predict how the walls will fare beneath the waves.
Innovations In Submarine Design
Innovation in design has continued to redefine what submarines can do. These advancements include:
Innovation | Impact |
Hydrodynamic Shapes | Enhances speed and maneuverability |
Composite Materials | Reduces overall weight, increases strength |
SONAR Advancements | Improves detection and navigation |
Submarines now also use stealth technology to remain undetected. The hulls incorporate features that minimize noise and avoid detection.
Each innovation isn’t just about going deeper or lasting longer underwater but also about ensuring the safety and effectiveness of the crew within.
Variations Across Types And Purposes
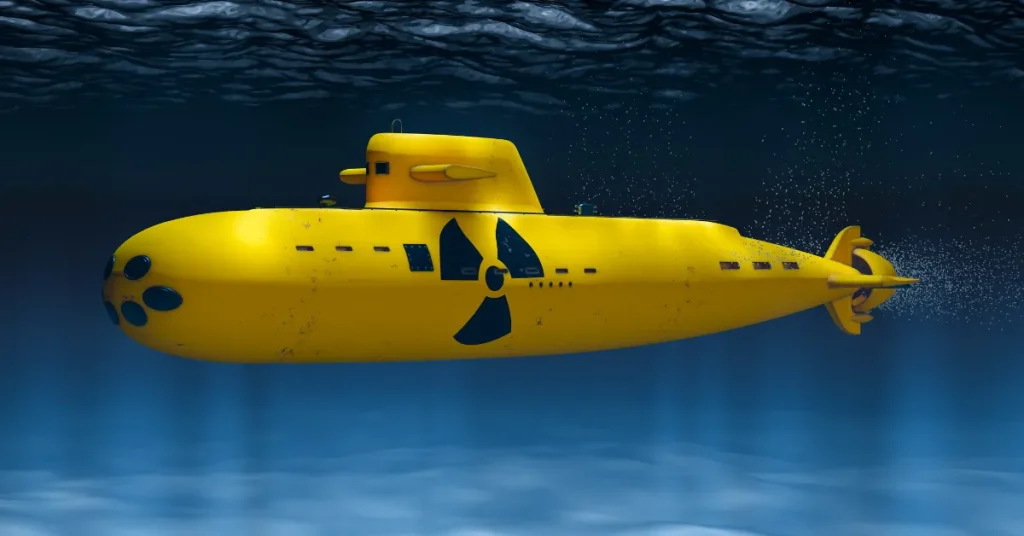
When diving into the depths of submarine design, wall thickness stands as a critical factor.
It is tailored to the vessel’s mission and operating environment. Let’s explore how construction varies in different types of submarines.
Military Vs. Research Subs
Military submarines are built for stealth and strength. Their walls can be exceptionally thick. This ensures they withstand high pressures at great depths. They also endure potential combat damage.
Research submarines, on the other hand, prioritize observation. Many have special features.
These may include transparent sections to view marine life. Wall thickness varies, balancing safety with observation needs.
Nuclear Submarines: A Special Case
Nuclear submarines operate under a unique set of conditions. They house reactors needing robust containment. Below, a breakdown summarizes the differences:
Submarine Type | Wall Thickness Purpose | Typical Wall Thickness |
Military (Diesel-Electric) | Pressure, stealth, and combat durability | ~20-25 cm |
Military (Nuclear-Powered) | Containment of nuclear reactor, extended patrols | ~25-33 cm |
Research | Balance of observation and safety | Varies widely |
It’s clear that design needs determine submarine wall thickness. Military vessels typically feature the thickest walls.
But the nuclear class takes robustness to the next level. Research subs often show a broader range in wall thickness. This is due to their specialized purpose. Every design balances the unique demands of the submarine’s intended role.
Maintenance And Upkeep Of Submarine Walls
Submarine walls are vital for the safety of submarines. They must stay strong under high pressure. Proper maintenance and upkeep guarantee this. Skilled teams check and fix these walls often. It keeps both the vessel and its crew safe underwater.
Routine Inspections
Regular checks are key to submarine wall maintenance. Inspections help find issues early. Teams look for cracks, corrosion, and abnormalities. These routines ensure quick fixes before they grow.
- Visual Assessments: Experts use cameras to examine exterior walls.
- Ultrasonic Testing: This detects wall thickness changes.
- Pressure Tests: These confirm the wall can handle deep sea stress.
Handling Repairs Underwater
Submarine wall repairs can happen below sea level. Special divers, known as saturation divers, perform these tasks.
Repair Type | Tools Used | Repair Time |
Patching Holes | Clamps, Underwater Welding Equipment | Varies by Size |
Sealing Cracks | Epoxy, Sealant | Several Hours |
Underwater welding and epoxy application are common methods. Divers must be careful with the submarine’s thick walls. Delicate operations prevent further damage.
Future Of Submarine Technology
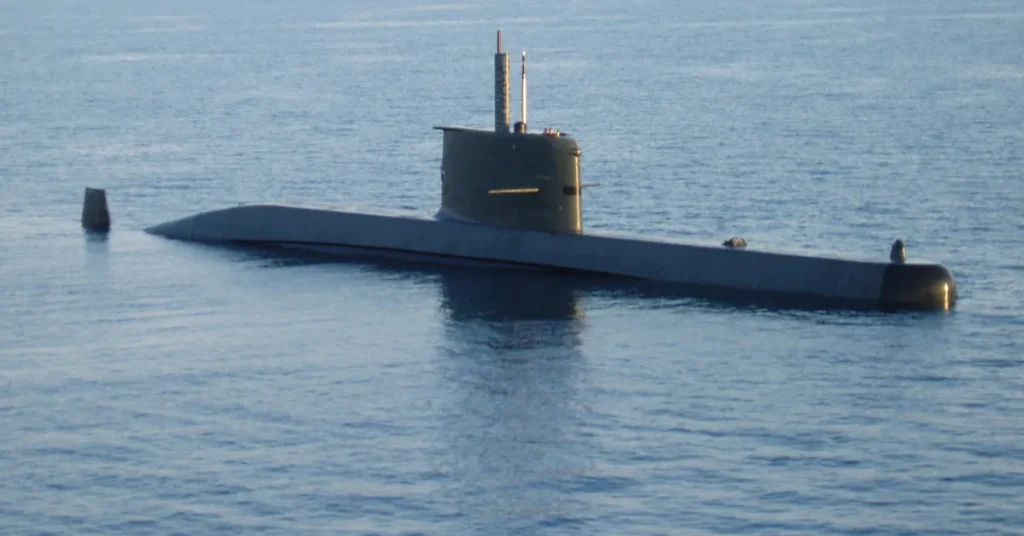
The future of submarine technology paints an exciting picture of innovation and strength. With every new model, these underwater vessels evolve to conquer the deep with enhanced features.
The walls of a submarine, crucial to its integrity, have transformed with time and technological advancements. Let’s dive into what the future holds for submarine construction and design.
Emerging Materials
Research and development in material science promise submarines that are not just strong but also lightweight. Scientists are exploring advanced composites and alloys that can withstand extreme pressures without adding excess weight. Such materials include:
- High-strength steel
- Titanium alloys
- Carbon fiber-reinforced polymers
These materials may lead to thinner yet stronger walls, allowing for more efficient designs. Improvements in welding and fabrication techniques are also integral to this shift.
Adapting To New Depths
The quest to explore new depths pushes submarines to adapt in structure. Increased depth requires walls capable of withstanding higher pressure. Engineers are considering various strategies:
Depth Range | Material Used | Wall Thickness |
Shallow Waters | Traditional Steel | Less Thick |
Mid-Level Depths | Advanced Steel Alloys | Moderately Thick |
Deep Waters | Exotic Materials | Thicker |
Durable materials like pressure-resistant titanium are crucial for new-generation subs. Innovative design adaptations also support submarines as they venture deeper into the ocean.
FAQs About How Thick Are Submarine Walls
How Thick Is Steel On Submarine?
Submarine hull steel thickness varies, typically ranging from about 0. 5 inches (13 mm) to over 3 inches (76 mm) for nuclear-powered vessels.
How Thick Are The Walls Of A Submersible?
The wall thickness of a submersible can vary, generally ranging from 1 inch to 4 inches, depending on the depth it’s designed to reach and the material used.
How Thick Is A Nuclear Subs Hull?
A nuclear submarine’s hull typically ranges from 2 to 4. 5 inches thick, designed to withstand deep-sea pressures.
What Are Submarine Walls Made Of?
Submarine walls, known as hulls, are typically made from high-strength steel or titanium. These materials withstand extreme underwater pressure and harsh oceanic conditions.
Conclusion
Understanding the thickness of submarine walls is crucial for marine safety. These steel barriers, usually between 2 to 11 inches, shield from ocean pressures.
This knowledge benefits engineers and submarine enthusiasts alike. Dive deeper into the subject for more insights into these impressive vessels’ construction.
Resources:
1. https://www.sublant.usff.navy.mil/About-Us/Submarine-Facts/